Optimising materials to create world class wind turbines

Categories: Materials Energy and sustainability
At over 80 metres in length, a single blade from a wind turbine is an impressive feat of engineering. Modern offshore wind turbine blades are now the largest fibreglass components ever cast in a single piece. This has been made possible through continuous improvement in materials development. The layering and structuring of fibreglass was originally a craft used for building the hulls of boats. Now, the design of composite materials – a group of materials which includes fibreglass – is done by international teams of engineers working together to create these record-breaking components.
Materials engineering is uniquely important to the design of wind turbines, particularly because there is so much of it! As the industry has grown, so has the size of our machines, with the largest now gathering wind from an area greater than three football pitches put together. The area that the blades sweep through is an important factor in turbine performance.
At a given wind speed, the amount of power which can be extracted from the wind increases by the square of the blade length – 3 times longer blades, 9 times more available power. However, if things are simply scaled up, the mass or weight of the blade increases by the cube of the length – 3 times the length, 27 times the mass! By making the blades longer, you can produce a lot more power. But if the amount of material is simply scaled up, the structure which supports them could never hold up such heavy components. Therefore, each time longer blades are created we must optimise the material structure to ensure a lightweight design.
While the basic ingredients of the composite material – fibreglass, epoxy resin and balsa wood – are not revolutionary themselves, the way in which they are woven, layered, and manufactured allows us to engineer a material with a combined weight, stiffness and cost that wouldn’t be possible using any single material alone.
That’s not to say that cutting edge materials don’t find their way into modern wind turbines. Magnets are a prime example. The generator which produces electricity within our offshore turbines does not require a transmission or gearbox to increase the rotational speed. Eliminating a gearbox is important for offshore turbines in order to bring down the overall weight and service costs, but the generator must operate at a high rotational force to account for the lower speed.
Permanent magnets are used to help achieve this; but these aren’t your everyday refrigerator decoration. Just a single magnet – about the size of a paperback novel – is strong enough to pick up a car! The magnets are mostly made of iron and boron, but their performance is improved by adding rare-earth elements like neodymium and dysprosium. While neodymium is available in relatively large quantities from a number of different sources, dysprosium is a much rarer material. As dysprosium is so rare, the cost of buying it fluctuates regularly. Finding new sources of the element could also negatively impact the environment through intensive mining operations. For these reasons, we are working to significantly reduce the use of dysprosium, without affecting the ability of the magnet to tolerate high temperatures.
We are taking on this challenge while at the same time improving the properties of the magnets, such as mechanical strength. These advances will enable our offshore wind turbines to operate at higher power in higher wind speeds. The importance of materials in wind turbine development is undeniable. Without research in materials technology, including composites and basic material research, it would be impossible for us to move towards clean energy. Materials engineering makes this possible, one small improvement at a time.
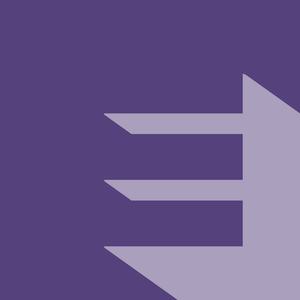